The Value of Utilizing a Chemical Defoamer in Different Applications
The application of chemical defoamers is an essential factor to consider throughout numerous industries, consisting of food handling, wastewater therapy, and drugs. These agents play a pivotal duty in mitigating foam development, which can prevent efficiency and compromise product top quality.
Comprehending Foam Formation
Foam formation is a complicated physical phenomenon that happens when gas bubbles are trapped within a liquid matrix, resulting in the production of a secure structure. This procedure can be influenced by different aspects, including the thickness of the liquid, the surface area stress at the gas-liquid user interface, and the presence of surfactants. Surfactants reduced the surface stress, promoting bubble development and stabilization, which usually causes the formation of foam in several commercial processes.
Foams are commonly come across in applications such as food production, wastewater therapy, and chemical production. In these contexts, foam can act as an insulator, hinder mixing processes, or prevent the performance of devices. The stability of foam is determined by the equilibrium in between the pressures acting to support the bubbles and those that promote their collapse.
Recognizing the technicians of foam formation is essential for properly managing its visibility in different systems. By understanding the underlying principles, markets can devise methods to mitigate unwanted frothing, thereby improving functional efficiency and product high quality. This foundational understanding acts as a forerunner to discovering the energy of chemical defoamers, which specifically deal with foam-related difficulties in countless applications.
Benefits of Chemical Defoamers
Chemical defoamers offer considerable advantages across different sectors by efficiently lowering and controlling foam development. One of the primary benefits is enhanced operational efficiency. By lessening foam, chemical defoamers aid keep optimum manufacturing prices and minimize downtime associated with foam management. This is particularly important in processes where extreme foam can impede machinery or interrupt process.
Additionally, chemical defoamers add to improved item quality. Frothing often causes disparities in solutions, which can negatively impact the last item. By managing foam degrees, defoamers make certain harmony, consequently improving the overall top quality of the outcome.
Cost-effectiveness is another notable advantage (Chemical Defoamer). By reducing the quantity of resources required for manufacturing and minimizing waste, chemical defoamers can result in significant financial savings. In addition, they usually permit lowered power intake, as procedures can run a lot more efficiently and need much less intervention.
Applications in Food Handling
In the food processing industry, reliable administration of foam is important to make certain both item quality and operational performance. Foam can disrupt numerous processes, from blending and mixing to packaging, leading to reduced returns and possible contamination. Chemical defoamers play an essential function in alleviating these issues by quickly breaking down foam, permitting smoother operations and boosted item uniformity.
In applications such as dairy handling, defoamers prevent excess foam formation during the production of milk, yogurt, and cheese, which can interrupt equipment and impact the structure of the final item. Similarly, in brewing and fermentation procedures, foam control is essential to maintain the stability of the beverage and guarantee optimum fermentation prices.
Furthermore, chemical defoamers are made use of in food sauces, dressings, and solutions to boost the security and appearance of the final products. By reducing foam during manufacturing, suppliers can achieve better mixing and diffusion of components, causing superior quality. In general, the consolidation of chemical defoamers in food processing is vital for maintaining performance, high quality, and security in food manufacturing.
Role in Wastewater Treatment
Efficient foam administration is equally important in wastewater treatment processes, where excessive foam can hinder procedures and complicate the treatment of effluents. In numerous wastewater treatment centers, foam can create as a result of organic task, surfactants, or other organic materials existing in the influent. This Full Article foam can cause a series of operational challenges, including lowered therapy performance, enhanced maintenance demands, and potential regulative compliance concerns.
Chemical defoamers play a crucial role in mitigating these obstacles. By minimizing the surface stress of the fluid, defoamers advertise the collapse of foam frameworks, therefore helping with smoother procedure of tools such as oygenation containers and clarifiers. Their timely application helps preserve ideal hydraulic problems, enhancing the overall performance of solids separation processes.
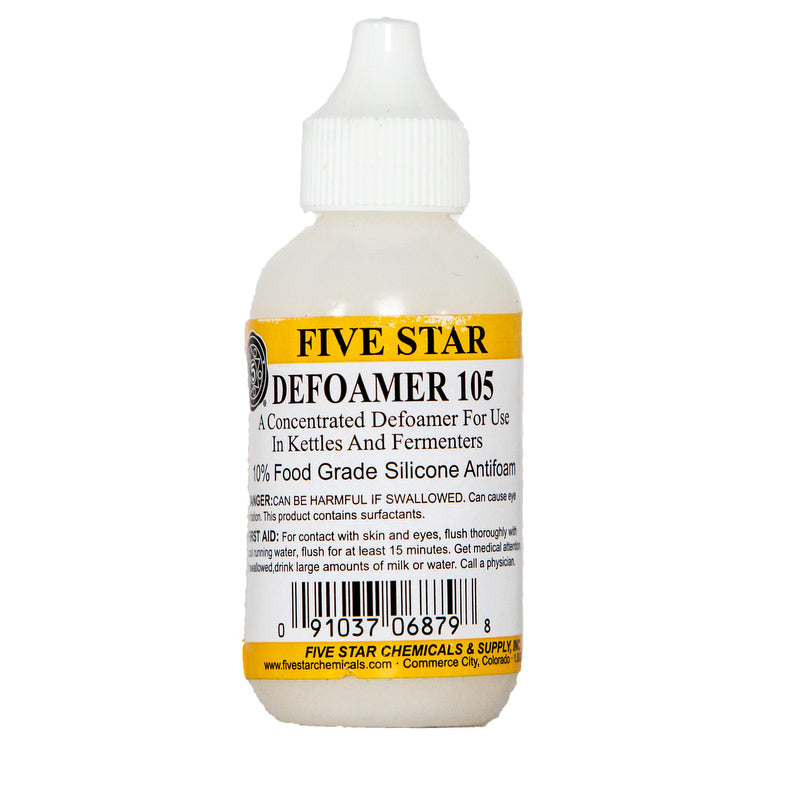
Influence On Drug Manufacturing
Foam control is critical in pharmaceutical manufacturing, where the presence of excessive foam can interfere with producing processes and compromise product top quality (Chemical Defoamer). The development of foam during different stages, such as blending, mixing, and fermentation, can lead to ineffective blending, insufficient heat transfer, and even equipment damage. These issues not only cause operational delays however can likewise trigger substantial monetary losses and influence compliance with stringent governing standards
Chemical defoamers are specifically formulated to mitigate these obstacles. By efficiently minimizing foam development, they boost procedure performance and maintain the integrity of the final product. Specifically, defoamers make certain regular dosage types, improve the stability of suspensions and solutions, and simplify cleaning procedures by stopping foam accumulation in equipment.
In addition, using defoamers can optimize the yield of active pharmaceutical components (APIs) by promoting far better extraction and filtration procedures. As pharmaceutical firms aim to boost product high click for source quality while decreasing production costs, the function of chemical defoamers becomes progressively vital - Chemical Defoamer. Their unification right into manufacturing protocols not just supports conformity with Great Production Practices (GMP) however also fosters advancement and competition in a rapidly advancing industry
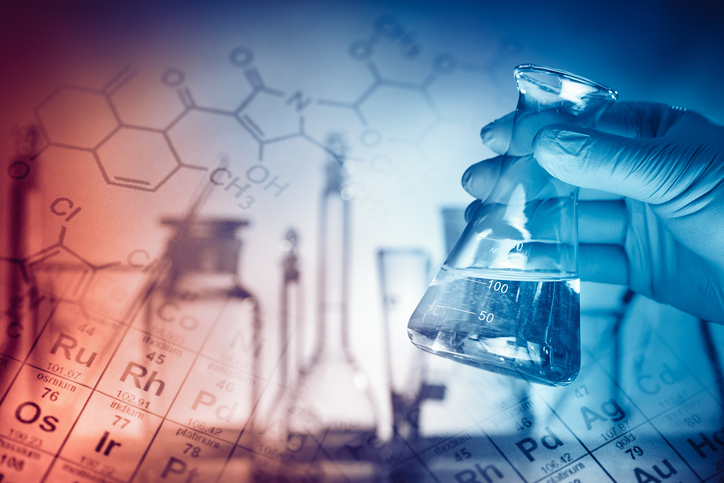
Verdict

Chemical defoamers offer substantial advantages across numerous markets by successfully controlling and reducing foam development. By lessening foam, chemical defoamers help preserve optimum manufacturing prices and lower downtime connected with foam administration. Chemical defoamers news play a critical role in minimizing these problems by promptly breaking down foam, permitting for smoother procedures and enhanced item uniformity.
Reliable foam management is similarly important in wastewater therapy procedures, where excessive foam can impede operations and complicate the treatment of effluents.Foam control is essential in pharmaceutical production, where the existence of too much foam can interfere with manufacturing procedures and concession product quality.